日用陶瓷自动施釉线
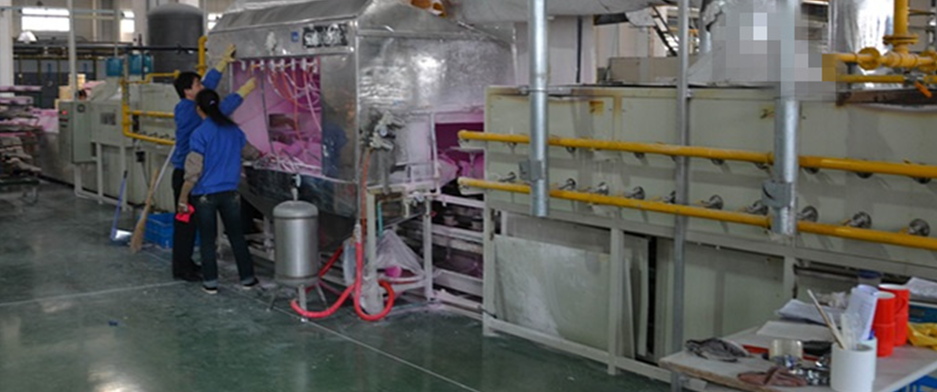
一、 用 途
1. Application
该设备主要应用于日用陶瓷两次烧成中,素坯施釉工段。能依次完成坯件输送,素坯预热,表面喷釉,釉后干燥,坯件冷却等工序。施釉线的传动采用链条式同步传动,速度可调。加热采用城市煤气(或其它燃气)明焰加热。
This equipment is mainly used for biscuit glazing working section in the two times of domestic ceramics firing. It could complete the working procedure in order, including blank transmission, biscuit preheating, surface glaze spraying, drying after glazing and blank cooling. Chain synchronous drive is used in transmission of glazing line and the speed is adjustable. City gas (or other fuel gas) direct firing is used for heating.
二、 技术参数
II. Technical parameters
1、型 号:
Type:
2、产 量: 30~65件/min
Output: 30~65 pieces/min
3、最大回转直径: 254 mm
Maximum rotating diameter: 254 mm
4、工 位 数: 129
Number of working station: 129
5、施 釉 方 式: 喷釉
Glazing method: Glaze spraying
6、链条运行速度: 9-20m/min
Chain operation speed: 9-20m/min
7、喷釉用压缩空气压力: 0.2-0.4 Mpa
Compressed air pressure for glazing: 0.2-0.4 Mpa
8、燃 料 种 类: 用户自选
Type of fuel: selected by users
9、装 机 功 率: 20kw
Installed power: 20kw
10、总 重:
Total weight:
11、外型尺寸: 长×宽×高
External dimension: length×width×height
三、 结构与工作原理
III. Structure and working principle
施釉线坯件主运动由主传动机箱、托架、链条、机架、从动机箱等部分组成,主传动为无级变速,链条的松紧可调。坯件施釉由预热、喷釉、烘干、冷却等部分组成,施釉是在坯件连续运动过程中进行。为了得到更好的施釉效果,适应不同的产品规格,保证釉面厚度均匀,在不同的工位设计了预热传动、喷釉传动、烘干传动等辅助运动。为了保证托架部分的清洁,避免釉料的粘结和堆积,影响坯件施釉质量,设计了清洗部分和清洗传动部分。为了充分回收釉料及控制工作环境污染,设计了湿法除尘装置,以保证尾气排放达标。坯件的上线和下线由工人手工操作完成。施釉线配有电气控制部分,在上线和下线的两端,安装有报警装置和急停按钮。该机的结构设计充分体现了安全、可靠、方便和环保。
Primary motion of blank of glazing line is composed of main driving box, bracket, chain, rack and slave driving box. Main driving is infinitely variable speed transmission and the tightness of chain is adjustable. Blank glazing is composed of preheating, glaze spraying, drying and cooling. Glaze spraying is carried out during continuous moving of blank. In order to get a better glazing effect, adapt to different product specifications and ensure the even thickness of glaze, some auxiliary motions such as preheating driving, glaze spraying driving and drying driving are designed at different working stations. In order to ensure the cleanliness of bracket part and prevent the bonding or accumulation of glaze and the influence on glazing quality, cleaning part and cleaning driving part are designed. In order to sufficiently recover glaze and control working environment pollution, wet dust extraction device is designed to ensure that exhaust gas emission reaches the standard. The on line and off line of blanks shall be completed by workers manually. Glazing line is equipped with electrical control part, and alarm device and emergency stop button are provided at both ends of on line and off line. The structural design of this device fully reflects the safety, reliability, convenience and environmental protection.